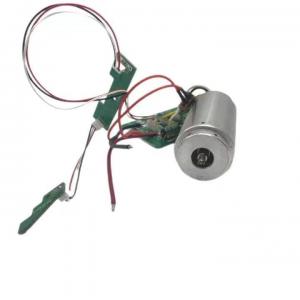
Add to Cart
Outer dimensions
Packaging & delivery
Port:SHENZHEN
Lead time:
Quantity(pieces) | 1 - 1000 | 1001 - 10000 | >10000 |
Lead time (days) | 15 | 30 | To be negotiated |
Essential details
Picture
A BLDC motor uses a simplified structure with trapezoidal stator windings.
Rotor A rotor consists of a shaft and a hub with permanent magnets arranged to form between two to eight pole pairs that alternate between north and south poles. Figure 6 shows cross sections of three kinds of magnets arrangements in a rotor. There are multiple magnet materials, such as ferrous mixtures and rare-earth alloys. Ferrite magnets are traditional and relatively inexpensive, though rare-earth alloy magnets are becoming increasingly popular because of their high magnetic density.
There are three classifications of the BLDC motor: single-phase, two-phase and three-phase.
This discussion assumes that the stator for each type has the same number of windings. The single-phase and three-phase motors are the most widely used. Figure 5 shows the simplified cross section of a single-phase and a three-phase BLDC motor. The rotor has permanent magnets to form 2 magnetic pole pairs, and surrounds the stator, which has the windings. N N S S A B Stator Rotor Permanent magnets Air gap N N S A B S C Rotor Stator Permane nt magnet Air gap (a) Single-phase (b) Three-phase—Simplified BLDC Motor Diagrams A single-phase motor has one stator winding—wound either clockwise or counter-clockwise along each arm of the stator—to produce four magnetic poles. By comparison, a threephase motor has three windings. Each phase turns on sequentially to make the rotor revolve. There are two types of stator windings: trapezoidal and sinusoidal, which refers to the shape of the back electromotive force (BEMF) signal. The shape of the BEMF is determined by different coil interconnections and the distance of the air gap. In addition to the BEMF, the phase current also follows a trapezoidal and sinusoidal shape. A sinusoidal motor produces smoother electromagnetic torque than a trapezoidal motor, though at a higher cost due to their use of extra copper windings.
Brushless motors use semiconductor switching devices to achieve electronic commutation, which replaces traditional contact commutators and brushes with electronic switching devices. A brushless motor consists of a permanent magnet rotor, a multi pole winding stator, a position sensor, etc. The position sensor exchanges the stator winding current in a certain order based on the changes in rotor position (i.e., detects the position of the rotor magnetic poles relative to the stator winding, generates a position detection signal, and the signal conversion circuit controls the power switch circuit. The winding current switches according to a certain logical relationship). The electronic switch circuit controlled by the position sensor output provides the working voltage of the stator winding.
Brushless motors have high reliability, no commutation sparks, low mechanical noise, and are widely used in high-end video recorders, video recorders, electronic instruments, and automated office equipment. It should be noted that many people believe that a brushless motor is a DC motor, which is why it is called a "brushless DC motor". In fact, a brushless motor is an AC motor, which is a three-phase AC permanent magnet motor.