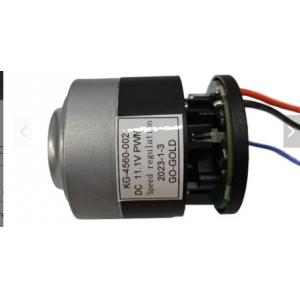
Add to Cart
Essential details
Packaging & delivery
KG-4560 brushless motor 24V output power 400w rated speed 110000RPM bldc mini wet dry vacuum cleaner motor 24v
Quantity(pieces) | 1 - 1000 | 1001 - 10000 | >10000 |
Lead time (days) | 15 | 30 | To be negotiated |
Voltage(V): | 18-30V | Torque(Nm): | 7-30 Nm |
Input power(W): | 60-400W | Rated speed(RPM): | 75000-115000RPM |
Brushless Direct Current (BLDC) motors are one of the motor types rapidly gaining popularity. BLDC motors are used in industries such as Appliances, Automotive, Aerospace, Consumer, Medical, Industrial Automation Equipment and Instrumentation. As the name implies, BLDC motors do not use brushes for commutation; instead, they are electronically commutated. BLDC motors have many advantages over brushed DC motors and induction motors.
A few of these are: • Better speed versus torque characteristics
• High dynamic response
• High efficiency • Long operating life
• Noiseless operation
• Higher speed ranges
In addition, the ratio of torque delivered to the size of the motor is higher, making it useful in applications where space and weight are critical factors.
BLDC motors are a type of synchronous motor.
This means the magnetic field generated by the stator and the magnetic field generated by the rotor rotate at the same frequency. BLDC motors do not experience the “slip” that is normally seen in induction motors. BLDC motors come in single-phase, 2-phase and 3-phase configurations. Corresponding to its type, the stator has the same number of windings. Out of these, 3-phase motors are the most popular and widely used.
The stator of a BLDC motor consists of stacked steel laminations with windings placed in the slots that are axially cut along the inner periphery (as shown in Figure 3). Traditionally, the stator resembles that of an induction motor; however, the windings are distributed in a different manner. Most BLDC motors have three stator windings connected in star fashion.
Each of these windings are constructed with numerous coils interconnected to form a winding. One or more coils are placed in the slots and they are interconnected to make a winding. Each of these windings are distributed over the stator periphery to form an even numbers of poles. There are two types of stator windings variants: trapezoidal and sinusoidal motors. This differentiation is made on the basis of the interconnection of coils in the stator windings to give the different types of back Electromotive Force (EMF).