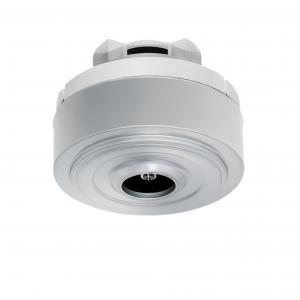
Add to Cart
Lead time:
Quantity | 1-1000 | 1001-10000 | ≥10000 |
Lead days | 15 | 30 | To be negotation |
Product Description
Rated Speed | 45000RPM | Rated Voltage | 48V |
Rated Power | 650W | Torque | Customizable |
Essential details
Rated Voltage: 48V
Rated Speed: 45000RPM
Rated Power: 650W
Commutation: Brushless
Application: Vacuum Cleaner
Weight: 0.75kg
Torque: Customizable
Max. vacuum eyapressure: 20.2kPa
Max. air flow: 2.53m3/min
Efficiency: 43%
Key Word: BLDC Motor
Warranty: 3 Years
Model Number: KG-6586DC48
Place of Origin: Guangdong, China
Drawing
Sample
Application
Brushless DC motors use electric switches to realize current commutation, and thus continuously rotate the motor. These electric switches are usually connected in an H-bridge structure for a single-phase BLDC motor, and a three-phase bridge structure for a three-phase BLDC motor. Usually the high-side switches are controlled using pulse-width modulation (PWM), which converts a DC voltage into a modulated voltage, which easily and efficiently limits the startup current, control speed and torque. Generally, raising the switching frequency increases PWM losses, though lowering the switching frequency limits the system’s bandwidth and can raise the ripple current pulses to the points where they become destructive or shut down the BLDC motor driver.
Torque or Commutation Loop The torque loop is used for sensorless applications to control the current through the motor. The torque is related to the current and therefore this feedback measures the current. A sense resistor measures the voltage and current sense amplifier senses the current and sends the signal to the ADC which digitizes the current and sends it to the controller. Measuring the motor current is often used as a safety feature. In case the motor is in a stalled position, the current increases dramatically. Because of this exceptional increase in current, the ADC values reach a current-limit level that causes the system to shut down.
Motor Advantages